
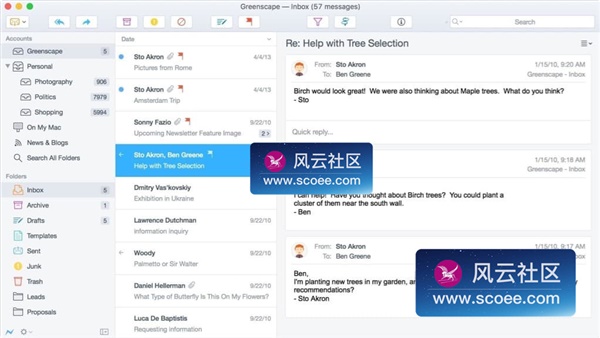
#POSTBOX FOR MAC PROGRAMMABLE SERIES#
Not what I was hoping for (although this means my POST Box will get another workout as I debug what's wrong!), but promising for Arcflash, as it means the series resistors don't appear to have broken anything *yet*īTW you were asking about my soldering process - I recorded a video of soldering up the first r3 POST Box a few days ago to show what's involved. Unfortunately the machine itself seems to have gone backwards a little since the last time I worked on it - it produced a weird pattern on screen when in the Arcflash bootloader, but managed to get into the self-test part of RISC OS 3 (purple then red, followed by black after a while). I fired up the first Arcflash v3 board in an A3000 today, and it worked as well as the v2 board that was in there already, so that was a success! it definitely wasn't as convenient as I would have liked, but it doing them by hand would have been even less fun! I would say that using a stencil, placing four 8-way resistor packs, reflowing, then cleaning up with wick was still quicker than placing 32 separate resistors would have been. Without a solder paste printer and a pick and place machine these parts are a lot more fiddly to use, it's possible to use them but it won't save any time. The problem with components like the smd resistor networks and smd chips with 0.5mm pin spacing is that in industry these parts are placed by machine on solder paste that's printed onto the pcb pads, before the reflow oven. I don't believe I ever fixed the spacing issue, although I did awkwardly solder four rows of bent header pins onto one board, which let me try it out on my RPC!
#POSTBOX FOR MAC PROGRAMMABLE HOW TO#
^ I've updated pretty much everything above tonight, so the build process should make a bit more sense now! Also figured out how to do a custom Arduino variant, so it'll identify on USB as "Arcflash" rather than "Circuit Playground Express" Then I do all the usual things: stick it on a lab PSU at 5V 0.2A to see if I missed any shorts, then plug in the J-Link, check voltages, program the bootloader, program the MCU firmware, program the CPLD (note that you don't need a Xilinx cable in fact there's no JTAG port exposed on the board, so you have to program the CPLD via the MCU), then build and program a set of ROM images into it. Make sure to check for bridges on the USB connector, as often they're hidden underneath a bit. the BGAs always seem to work out fine, but anything with 0.65mm or 0.5mm pins seems guaranteed to have at least one bridge. Finally I fire up the soldering iron and wick up all the solder bridges, of which there are usually many. at that point I turn off the power and pick it up with tweezers and set it on the raised corner of the hot plate to cool down for a few minutes. Usually this is just when the board starts to smoke a tiny bit.


Then it all goes on a little electric hot plate at some indeterminate temperature for a bit: I put it on the 300 degree setting and wait until the paste on the last component stops bubbling. hopefully still in the UK?) and very carefully place everything with a pair of tweezers, using an OptiVisor DA-4 so I can actually see what's going on. The stencil makes it all possible I use Chip-Quik leaded solder paste (available in the US. What's the status of the RiscPC/A30x0 adaptor? I can't quite follow from the posts in this thread if the spacing issue was resolved one way or another - I'd be quite keen on trying in RiscPC, A30x0 and A4000. I've now kitted to make up all 5 boards (was just planning on a couple originally) and plan to test on A3000, A300 and A400 boards initually. I've not sorted out the plan for soldering the BGAs yet and DHL lost my stencil - just arrived today and Xilinx programmer still en-route.
